Contents
In the ever-evolving landscape of construction, one method has been steadily gaining momentum for its efficiency, sustainability, and versatility: modular construction.
Once regarded as a niche approach, modular construction has now emerged as a disruptive force, reshaping the way we build everything from residential homes to commercial complexes. Yet, amidst the buzz surrounding this innovative technique, there remains a crucial gap in understanding among developers. What exactly is modular construction, and why should developers pay attention to it?
As expected, there are unique details about modular construction at each of the phases that remain a mystery. We’re here to demystify.
The Value of Repeatability
The most defining characteristic of modular construction is the use of a factory. Using a factory allows for a streamlined assembly-line process that not only facilitates rigorous quality control but also shortens the construction timeline by months.
As most would expect from a factory, repeatability is a must. In the context of modular construction, this means ensuring that each module produced adheres to consistent specifications and standards. But this does not mean that your project will be cookie-cutter.
Modular manufacturers will often have a library of pre-designed plans that can be configured to match the vision and needs of every client. When building with modular construction, especially when you have multiple projects, nailing a balance of repeatability and variability is a must.
When you work with a modular manufacturer like Volumetric Building Companies (VBC), your designer will sit down with you to narrow down where changes will be beneficial, and which can be standardized across projects for efficiency and consistency. This collaborative approach ensures that while each project may have unique requirements, the manufacturing process can still leverage standardized components and processes wherever feasible, optimizing both quality and cost-effectiveness. The goal is to provide standardization where it adds time and cost benefits in manufacturing and provide customization where it adds high value to the building design.
An area of the building that benefits from high customization is the exterior facade. Even with standard unit layouts, the exterior can be designed in accordance with the client's specifications and aesthetic preferences. This customization can range from various facade materials and colors to architectural details and building articulation, ensuring that each modular building seamlessly integrates into its surroundings and reflects the desired design style.
You Can View a Life-Size Prototype
Another benefit of the factory setting of modular construction is the ability to see a full life-sized prototype of a module before manufacturing fully kicks off for your whole project.
This prototype is fully finished and allows clients to experience the spatial layout, interior design, and overall feel of the module firsthand. This opportunity for inspection and feedback ensures that any necessary adjustments can be made early in the process, minimizing costly changes during mass production.
It’s also not just a prototype module. The prototype is usually the first in the series module, so if all is approved, the prototype will be included in the final product. Nothing is wasted.
Another significant benefit to the client is the assurance of consistency and quality throughout the entire project. Since the prototype serves as the first in the series module, its inclusion in the final product guarantees that the client will receive exactly what they expect and approve. This minimizes the risk of discrepancies between the prototype and the rest of the modules, ensuring a cohesive and satisfactory end result.
Your Project Might Not Be Subject to On-Site Inspections
Many states have a factory-built housing code that states if a structure is built in a factory, the portion that is built in a factory is not subject to on-site inspections. All necessary inspections are done in the factory.
This regulation offers a significant advantage to projects utilizing modular construction methods. By conducting all inspections within the controlled environment of the factory, potential delays and disruptions associated with on-site inspections are minimized or even eliminated entirely.
Centralizing inspections within the factory setting ensures consistent adherence to quality standards across all modules. Factory inspections are conducted under controlled conditions, allowing for thorough scrutiny of each component's construction, installation, and compliance with regulations. This meticulous oversight helps to mitigate the risk of errors or defects, ultimately enhancing the overall safety and reliability of the completed structure.
Most Size Constraints Come From Transportation
While factories will have size constraints when it comes to the height, length, and width of their modules, the limitations ultimately come down to transportation in both the US and Europe.
For example, for module widths, California law requires that any modules wider than 16 ft. must have a California Highway Patrol (CHP) escort when transporting. For this reason, at VBC, we keep our modules at 15 ft. 9 in. to ensure we don’t cross that max height threshold and incur higher costs for our client.
Transportation costs are partly calculated by the number of trips. This is where being strategic with the size of modules comes into play.
Let’s say you have two 40 ft. modules that need to be transported. Typically, the max size that can be fit on one truck is 70 ft, and can sometimes be as long as 73 ft. Since loading the two modules would exceed this max size, the modules will need to be taken on separate trucks and you’ll then be paying for an additional trip. An easy solution is to design the modules down to 35 ft. length so that both can fit on one truck.
Experienced modular manufacturers will know these details and work them into the design well before manufacturing begins, saving you time and money.
Working with the Right Modular Manufacturer Has Its Perks
The final note we want developers to know about is permitting. Some local planning departments are slow to recognize modular construction as a viable and efficient building method. Despite being around since the 60s and its numerous advantages to creating affordable housing, this reluctance to embrace modular methods may stem from unfamiliarity with the technology or traditional biases towards conventional building practices.
As a result, you may receive some pushback when trying to get your permits. This is where working with a well-established modular manufacturer with a long and positive track record is going to make a world of difference. Our team at VBC has been working to educate local planning departments about the benefits and reliability of modular construction. We have a proven track record of successfully navigating the permitting process and obtaining approvals for modular projects in various jurisdictions.
When you partner with us, you gain access to our expertise and establish relationships with regulatory authorities, streamlining the permitting process and minimizing delays. Our commitment to transparency, quality, and compliance ensures that your project meets all regulatory requirements while maximizing efficiency and cost-effectiveness.
Get in touch with our team today to see if modular construction is the right choice for your next project.
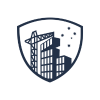