Contents
Volumetric Building Companies (VBC) has been a frontrunner in large-scale modular construction for a decade now, having produced some of the largest and most successful multi-unit structures all over the East Coast. From hotels to affordable apartment buildings, VBC has made its mark in the construction industry and continues to bring a positive light to modular construction. And now, VBC is bringing that spark to the West Coast.
With the opening of its first California modular factory in 2022, VBC is bringing a much-needed construction method that delivers quality products in a fraction of the time. With the cost of living in the Golden State continuing to rise, especially in the Bay Area, this development couldn’t have come sooner.
Right Place at the Right Time
VBC had been looking to expand to the West Coast for some time, and when an opportunity to do so materialized, COO Sam Tikriti says they had to jump on the moment, “The opportunity came in unexpectedly, so we decided to capitalize on it. The facility had the location, the size, and the equipment, and it made sense to us to accelerate a move to the West Coast.”
The purchase of the 577,000 sq ft factory came shortly after the closure of Katerra, a panelized modular manufacturer in Tracy, CA. Panelized modular differs in some ways from regular modular construction, so they knew it would take some time to restructure the factory to fit their needs, but that was a challenge worth taking on when you consider what a great deal they landed. “It was a $25 million transaction on what was considered to be a $110 million investment initially by Katerra,” says Tikriti.
VBC’s initial inventory assessment revealed that substantial restructuring was needed to optimize the acquired equipment and square footage fully. VBC is committed to streamlining processes, enhancing efficiency, and maximizing the value of the technology and equipment at their disposal.
Amidst the restructuring efforts, VBC discovered a silver lining. Some of the remaining equipment, particularly those designed for building cabinets, presented an opportunity to open new revenue streams. By selling cabinets to third-party customers, VBC not only found a profitable outlet for these resources but also expanded its reach in the industry.
Wrapping up the factory makeover, they rehired several former Katerra employees. These employees, familiar with the technology and processes, seamlessly integrated into VBC's operations. All they needed was training on the new processes and equipment, which wasn’t a far departure from Katerra’s.
Success with the California Modular Factory so far
Less than two years after acquiring the factory, VBC is already producing modules at a profit.
Most factories of this size would take up to five years to see profits, but VBC’s efficiency in utilizing as much of the factory as possible has given them a leg up.
VBC has also already completed its first West Coast project, a five-story building built over a podium in Oakland, California. This 44-unit apartment building is just over 67,000 square feet. VBC is off to a strong start in the West Coast market having completed this structure with close to zero tolerance issues.
At the heart of VBC's success lies the efficiency of its production lines, including the modular production line. This system has been fine-tuned to deliver modules with unmatched efficiency and quality.
How it Works
VBC's California modular factory boasts two core automated production lines, each playing a crucial role in streamlining the construction process.
One of these lines handles floor, wall, and ceiling assembly, significantly reducing production time. The production of a single wall is completed in as little as five to seven minutes, a fraction of the time it would typically take in on-site construction, representing an efficiency gain of approximately 85%.
At the heart of the factory lies a commitment to automation and precision that sets them apart. Their factory boasts state-of-the-art automation, fusing deep-rooted U.S. construction knowledge with top-of-the-line European manufacturing equipment. It's this dedication to merging the best of both worlds that propels VBC toward continued success in the modular construction landscape.
VBC employs a unique tool - the "modular benefit scorecard" - to determine whether a project is an ideal fit for the factory. This score, driven by precision and data gathered through a short quiz assesses the potential build and ensures that the right projects are selected for production further optimizing efficiency and project success. Those efficiencies can be passed onto the developer in the form of cost and time savings.
California modular factory opens new opportunities for the West Coast
With this new West Coast modular factory, VBC has been able to open its full-service process to all of California. The California factory is able to produce up to 25,000 square feet of housing a week on a single shift.
VBC’s California Modular Factory can produce:
- Market-Rate Apartments
- Affordable Housing
- Student Dorms
- And low-rise hotels
VBC's California modular factory has provided them with the capacity to place a more substantial emphasis on affordable housing projects, with these endeavors now comprising a significant 50% of their project pipeline.
By dedicating a substantial portion of its efforts to affordable housing, VBC gains access to a broader spectrum of funding opportunities, government grants, and favorable interest rates. This strategic pivot is not just a business move; it's a commitment to addressing a pressing societal need.
One of the critical factors that have enabled VBC's success in the West Coast market is the level of cooperation and support they've received from local authorities and jurisdictions. The relationships forged during permitting processes have proven to be instrumental in expediting projects and ensuring a smooth construction process. This collaboration with local authorities has streamlined the often complex permitting procedures.
VBC’s plan for the future
Following the success of the California modular factory, VBC has high hopes to open more modular factories throughout the US and even more overseas such as in the Middle East.
As VBC looks ahead, its commitment to efficiency, quality, and affordability in modular construction remains unchanged, setting a course for a future where high-quality, accessible housing and construction innovation stays within reach where it's most needed.
The new factory has vastly opened up VBC’s bandwidth and capabilities up and down the West and East Coast. Take our modular benefit quiz to find out if your next multi-unit project can be built in one of our state-of-the-art factories.
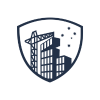