Contents
The affordable housing crisis has reached a tipping point, dominating headlines and sparking urgent calls for action across the nation. The statistics are sobering: the average cost of a home in the U.S. has soared to $412,000, a staggering 128% increase since 2000.
Nowhere is this crisis more acute than in California. The state faces a housing shortage of unprecedented proportions:
-
3.5 million new units are needed by 2025 to meet demand.
-
Construction costs for affordable housing often exceed $500 per square foot, making development increasingly unsustainable.
-
Cities like Los Angeles, San Francisco, and San Diego have declared housing emergencies, underscoring the urgent need for scalable solutions.
At VBC, we’ve made addressing the affordable housing crisis a core focus. We believe that solving this challenge requires innovative approaches that balance cost, efficiency, and sustainability. By leveraging modular construction and productized design, we aim to deliver affordable, high-quality housing at scale to meet the needs of communities most impacted by this crisis.
This work led to VBC being awarded an Ivory Prize, which is an annual award recognizing ambitious, feasible, and scalable solutions to housing affordability.
Lead with a Productized Approach That Scales
At VBC, we’ve invested significant resources into developing affordable housing as productized solutions that balance client flexibility with the speed and efficiency of factory manufacturing.
Our approach, called 80Mods, is rooted in the principle of delivery productization:
- 80% Standardized: Modules are pre-engineered for maximum production efficiency, ensuring consistency, quality, and speed.
- 20% Flexible: Modules are adaptable to the unique requirements of each project, allowing for customization without sacrificing efficiency.
This model enables us to tailor solutions to meet specific needs while maintaining cost efficiency and high manufacturing performance.
By prioritizing repeatability, productization drives:
-
Faster Results: Streamlined processes shorten timelines, enabling quicker project delivery.
-
Lower Costs: Standardized designs and bulk manufacturing reduce overall expenses.
-
Scalability: This approach supports rapid scaling, allowing developers to address the growing demand for affordable housing effectively.
VBC’s productized approach ensures high-quality outcomes at scale, helping clients meet housing needs faster, more affordably, and without compromising on flexibility or performance.
Affordable Housing in Action
At VBC, we take pride in delivering real, impactful projects that address the urgent need for affordable housing. These aren’t just concepts or renderings, they’re communities making a difference today.
Veteran’s Village, Philadelphia
In May 2023, VBC completed Veteran’s Village, a 47-unit permanent housing community dedicated to supporting veterans. This transformative project not only provides safe, affordable homes but also exemplifies innovation in affordable housing.
The design has been made open-sourced, allowing other developers to replicate it and expand the availability of affordable housing nationwide.
Townhomes with HACE
In collaboration with HACE, a Philadelphia-based community development group, VBC delivered a series of two-story townhomes as part of an affordable multi-family housing development in Philadelphia’s outer city. This project combines thoughtful design with affordability to support the community’s housing needs.
Sustainability Built In
While the speed of modular construction often garners the most attention, sustainability is a cornerstone of this innovative building method. A recent study in Nature highlights the environmental benefits of modular construction:
-
74% reduction in material waste compared to traditional construction methods.
-
58% reduction in emissions from construction activities.
At VBC, we’re committed to going beyond the industry standard for sustainability, integrating practices that reduce our environmental impact while driving innovation.
Projects, like Village Square on Haverford blend affordable housing with sustainable goals. This development, which will finish in January of 2025, is part of the nation’s Green Building Program, which outlines resilience criteria that helps better prepare homes to withstand local climate hazards.
Powering Progress with Renewable Energy
Our state-of-the-art factory in Tracy, California, is powered entirely by 3,200 solar panels, generating 1,700 megawatt-hours of electricity annually—enough to power 900 homes each year.
Recycling for a Greener Future
-
Drywall Recycling: VBC recycles 420 tons of drywall annually, equivalent to the weight of 10 herds of elephants. These offcuts are sent to drywall producers, who grind and reuse the material, keeping it out of landfills.
-
Lumber Upcycling: Our Tracy factory diverts 1 ton of lumber per day from landfills. Partnering with circular economy innovators, we upcycle these cutoffs into engineered wood and studs, turning waste into valuable building materials.
At VBC, sustainability isn’t just a byproduct of modular construction, it’s a driving principle. By embracing renewable energy, waste reduction, and recycling, we’re building more than homes; we’re creating a blueprint for a more sustainable future.
Innovation, Repeatability and Sustainability
The challenges of the affordable housing crisis require bold, scalable, and sustainable solutions. At VBC, we’ve embraced this challenge by pioneering a productized approach to modular construction that delivers faster, more affordable, and higher-quality housing at scale.
By blending innovation, repeatability, and sustainability, we’re not just building homes, we’re building a better future for communities most impacted by the housing crisis. From projects like Veteran’s Village, which provides life-changing housing for veterans, to forward-thinking developments like Village Square on Haverford, designed to meet Green Building Program standards, VBC is committed to making a lasting impact.
Our focus on sustainability goes beyond industry norms, incorporating renewable energy, waste reduction, and circular economy practices at every step of the process. This commitment ensures that the homes we build today not only meet the needs of our communities but also contribute to a more resilient and sustainable tomorrow.
We’re proud to be recognized with awards like the Ivory Prize for our efforts, but our greatest achievement is the difference we make in people’s lives. Together, we can redefine what’s possible in affordable housing, creating innovative, sustainable solutions that scale to meet the demands of today and tomorrow.
---
Talk to a VBC representative to see if modular construction is right for your next large-scale project.
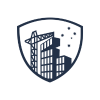