Contents
Modular construction is fast growing in popularity amongst developers for its speed, efficiency, and versatility. Thanks to new technology and engineering research, this construction method has evolved since its beginnings to now being used for large-scale projects that hold 500+ living units.
However, some are skeptical of its ability to stand the test of time. How can a construction method that cuts down timelines by up to 50% produce structures that are durable and long-lasting?
Quite easily actually.
In fact, Volumetric Building Companies (VBC) have been erecting these large buildings for over a decade now, and all completed projects show no signs of crumbling any time soon. You can learn more about our construction methods here.
How Long Do Modular Structures Last?
Large-scale construction projects can last 100+ years, approximately the same as projects built with traditional construction.
The longevity of modular structures is further bolstered by the adaptability of their design. Modular buildings can be easily upgraded, expanded, or repurposed to meet changing needs, providing a sustainable and future-proof solution.
As technology and construction methods continue to advance, modular structures remain at the forefront of the construction industry, assuring not only durability but also flexibility in the face of housing shortages and a dwindling construction labor market.
Factors Influencing Longevity of Modular
Some people are turned off by the concept of “factory-made” homes, but the factory setting plays a large part in ensuring these buildings are built to last.
Higher Quality Control
Unlike traditional construction where unforeseen problems can arise at every step, modular factories have strict procedures in place to ensure a streamlined process and consistently high quality.
The controlled environment of a modular construction facility minimizes the impact of external factors, such as weather delays and damage, which often lead to quality issues in traditional construction.
Each module undergoes rigorous inspections and testing during the manufacturing process, adhering to stringent quality control measures. This meticulous attention to detail not only enhances the overall quality of the modular structure but also significantly reduces the likelihood of defects or inconsistencies, greatly expanding the lifespan of the structure.
Built for Transportation
People often forget about the phase that happens between the factory and installation at the site: transportation.
As most are aware, highways are riddled with potholes and other rough terrain that shake up cars and their occupants.
To withstand the jostling and vibrations during transportation, modular structures are designed and engineered with robust materials and construction methods. From reinforced framing to secure fastenings, every element is crafted with the understanding that it will endure a journey to the final destination.
This focus on transportation durability not only ensures that the modules arrive intact but also contributes to the overall strength of the modular structure once assembled on-site.
Stronger Materials
An essential element contributing to the durability of modular structures is the use of stronger materials.
For years, construction materials have been designed to suit the constraints of traditional on-site building methods.
By customizing raw materials and components specifically for the manufacturing environment, modular construction can significantly minimize waste and enhance overall efficiency while contributing to the overall strength and resilience of the completed modular structure.
Specialized Labor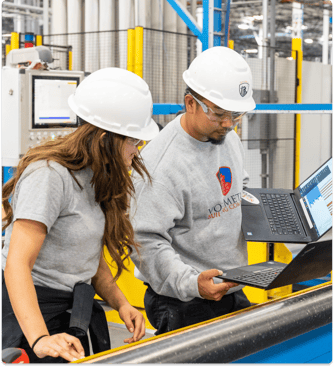
Unlike the diverse skill set required for on-site construction, modular assembly lines are manned by teams of experts, each mastering specific tasks within the manufacturing process.
This focused expertise ensures a higher level of precision and quality at every stage, from crafting individual modules to the final assembly on-site.
This specialization not only enhances efficiency but also significantly reduces the margin for error, resulting in structurally sound, meticulously crafted buildings.
FAQs
Are modular buildings more susceptible to wear and tear over time?
No, modular-built structures withstand the same wear and tear as traditional construction.
Due to the rigorous quality control measures in modular construction, these buildings often exhibit strong durability.
Do modular structures require more maintenance compared to traditional construction?
Depending on the building materials used, modular structures require the same maintenance as buildings constructed traditionally.
Maintenance needs can be influenced by factors such as specific materials used, environmental conditions, and the level of ongoing care.
How much time does modular construction save?
Modular construction can cut down traditional construction timelines by up to 50%.
When dealing with large-scale projects like a hotel or affordable housing complex with 100+ living spaces, this time efficiency can save developers hundreds of thousands of dollars.
Cutting a project from a two-year timeline in half means that developers can eliminate expenses like permitting fees, labor, and more by a year.
Is modular construction worth it for my project?
Considering the numerous benefits of modular construction, including efficient timelines and costs, high-quality control, and durability, many find it a compelling option for a wide range of projects, especially large-scale projects.
To determine if modular construction is the right fit for your specific needs, it's crucial to assess factors such as project size, complexity, and desired timelines.
Talk to a VBC representative to see if modular construction aligns with your project goals. Our experts can provide tailored insights, answer your questions, and guide you through the process.
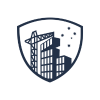